Servosila Robotic Arms
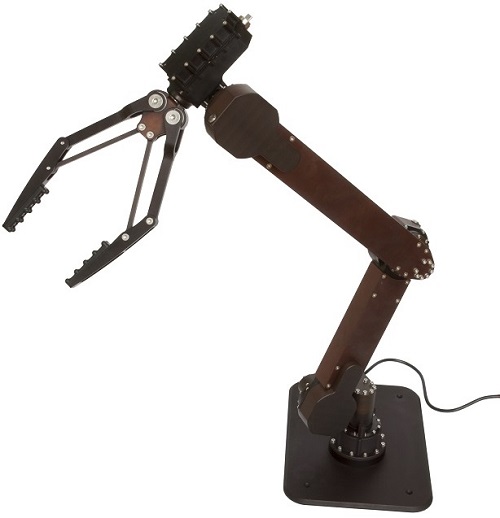
Servosila Robotic Arms are attachable payload modules for mobile service robots or other robotic platforms.
The robotic arms are typically mounted on a chassis or a torso of a mobile robot and powered by an on-board power supply system of the host robotic platform.
The robotic arms can be used both outdoors and indoors. The arms are water-tight, dust-proof and function properly in the rain and in the snow.
The robotic arms are designed to withstand impacts, collisions with obstacles and, in general, the harsh treatment so common to mobile robotics applications.
All-Weather Robotic Arms
In contrast to traditional industrial robotic manipulators, Servosila Robotic Arms are designed to operate in outdoor environments.
The servo actuators and external electrical connectors of the robotic arms are water-tight and dust-proof (IP68 rating). The entire arm can be occasionally submersed in water without any adverse effects on its performance. The robotic arms may be operated in cold or hot weather.
Designed for Outdoor Mobile Use
The harsh nature of outdoor mobile robotics applications caused a profound effect on the design of Servosila Robotic Arms, especially on the internal structure of servo actuators and their harmonic reduction gears. Mobile robots tend to bump into things and hit obstacles while on the move. Due to their designs, Servosila Robotic Arms can be exposed to a much harsher treatment than most traditional industrial robotic manipulators could possibly tolerate outdoors. There are no exposed cables on the outside of the robotic arms that could be torn off when a mobile robot moves through bushes or forests. Numerous protection measures built into electronic servo controllers and mechanical parts of Servosila Robotic Arms ensure reliable operation on-board of outdoor mobile service robots.
Lightweight Robotic Arms
Servosila Robotic Arms are lightweight by design. For a given lifting capability, Servosila Robotic Arms have a significantly lower weight than their industrial counterparts.
The lower weight of a Servosila Robotic Arm enables a mobile robot equipped with the arm to operate longer on a single battery charge, keep its center of gravity lower for better balance, climb stairs easier or have a superior mobility.
Unregulated Power Supply
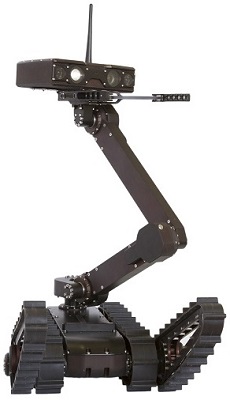
An unregulated DC power supply is all that is required to power a Servosila Robotic Arm on board of a mobile robot.
Since most mobile service robots are powered either by a battery or by a power generator (including hybrid-electric), the available on-board electric power might be scarce or unstable. Servosila Robotic Arms have special provisions that enable them to operate under such challenging conditions.
For convenience, every Servosila Robotic Arms also comes with a 220/110V AC power supply unit. The unit makes it possible to use the robotic arms in an office or laboratory settings without attaching the arm to a host mobile robotic platform.
Powering the arm from a wall socket is useful when developing software or for a tabletop demonstration at a conference or an exhibition.
CANbus and USB Control Interfaces
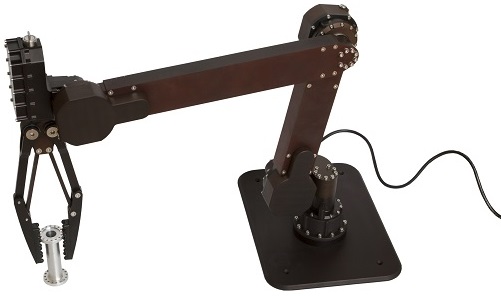
Servosila Robotic Arms are controlled via a CANbus network interface with a CANopen application protocol. An on-board control computer/controller of a host mobile robot uses a CANbus network to send commands to individual servo actuators of the robotic arm and to receive execution reports and telemetry back from the servos.
For convenience, an external USB-to-CAN adapter (dongle) is supplied with all Servosila Robotic Arms. The adapter allows controlling the robotic arms from a regular PC/laptop computer via a USB port. This is useful for live tabletop demonstrations or for system prototyping using a laptop computer connected to both a robotic chassis and a robotic arm at the same time.
Robotic Arm Software
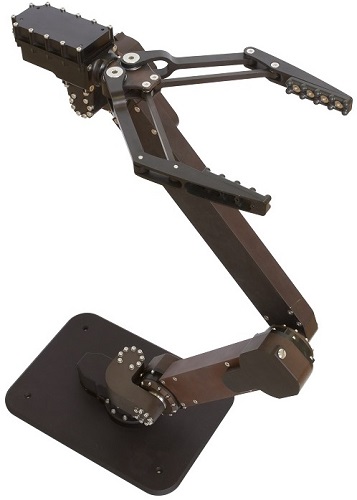
An on-board control computer of a host mobile robotic platform might run either Linux or Windows or no operating system at all as long as the computer has a CANbus network interface. No special drivers are required to be installed on the control computer of the mobile robot to programmatically control a Servosila Robotic Arm via its CANbus interface.
A software package for ROS, an open source robotic operating system, is freely available online for those programmers or researchers who prefer using ROS to programmatically control the arm.
All Servosila Robotic Arms come with a package of software tools required for configuring, testing, health-checking and fine-tuning the arms. The software shall normally be installed on a laptop computer or a PC that gets connected to the arm via a USB-to-CAN adapter whenever the arm needs to be serviced.
General-Purpose Grippers
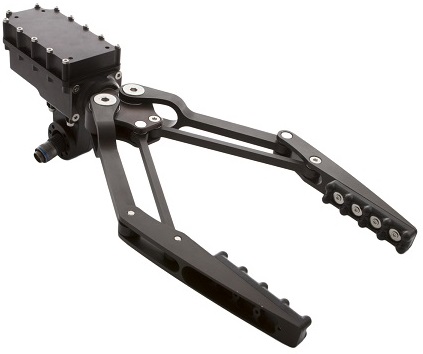
Servosila Robotic Arms are equipped with either a rotating or a non-rotating gripper optimized for grabbing objects from the ground or from various heights. Opening doors by rotating the door handles is a key design use case. The grippers might have provisions for installing additional instruments such as dirt digging claws or drills.
Choose a rotating gripper over a regular gripper, if a target application calls for opening doors by rotating door handles, or if an extra degree of freedom of the gripper is required for precise object manipulation. The gripper can also be excluded from the configuration, if the arm of the robot is to be used for carrying mission-specific payloads, for example, flame-retardant grenades or ground- or wall-penetrating radars, rather than for object manipulation.
The fingers of the gripper come with hardpoints for connecting external tools. The hardpoints on the fingers and on the chassis come handy when the robot needs to be adapted for a specific remote engineering operation. For example, special claws at the tips of the fingers of the gripper enable the robot to drag suspicious objects such as left bags, cut open holes, or gently open the bags. The claws also enable the robot to dig dirt or pick objects hidden under piles of rubbish. The claws are optional and field-installable.
Connectors for External Payload Modules
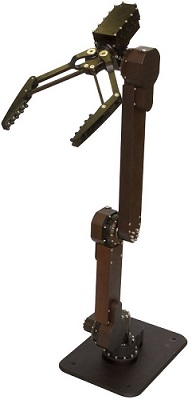
Servosila Robotic Arms feature a watertight socket at the gripper end of the arms. The socket is intended for connecting additional payload modules such as video cameras, infrared sensors, touch sensors or entire robotic heads that extend functionality of the arm. Those external modules are mounted on the robotic arm and connected to the control computer of a host mobile platform via a special cable hidden inside the arm.
The special payload cable goes through the inside of the robotic arm from the watertight socket at the gripper end of the arm to another watertight socket at the base of the arm where an external cable that interconnects the arm and a control computer of a mobile robot is attached.
This way a control computer installed in a robotic platform can control a payload module mounted at the end of a Servosila Robotic Arm.
Small Onboard Footprint
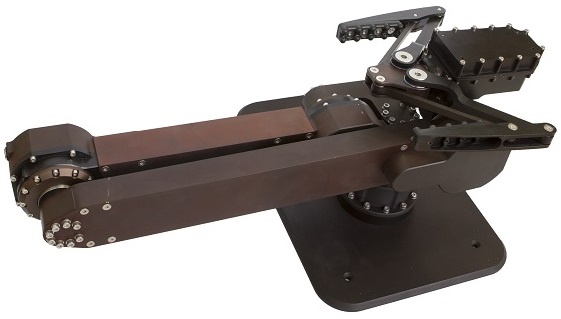
When not in an active use, Servosila Robotic Arms can be folded into a very compact form that doesn’t occupy much space on the top of a robotic chassis or on the side of a torso. This feature protects the robotic arm of a mobile robot in case of an unexpected collision with an obstacle or whenever a rough terrain is encountered by the mobile robotic platform. The compact folded form also comes handy during transportation. By folding its robotic arm into the compact form, the robot frees up its working area for other payloads to operate in. This is useful in case the robot is equipped with additional payloads other than the robotic arm.
Intelligent Servo Actuators
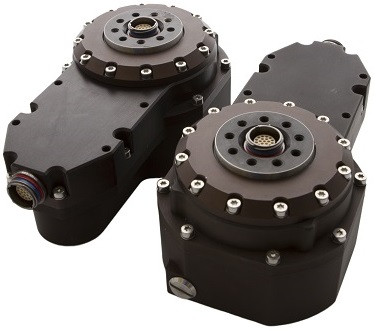
The main components of any Servosila Robotic Arm are servo actuators that actuate each degree of freedom of the arm. Designs of the servo actuators are based on a harmonic reduction gears technology and a field-oriented BLDC motor control principle.
Each of the servo actuators features a microprocessor-based controller that commands the actuators’s shaft either in a “servo mode” or in a “speed mode” or in a “torque mode”. The built-in servo controller receives commands via a CANbus network from an on-board computer of a host mobile platform, executes the commands and sends telemetry back to the host platform.
Each servo actuator features multiple built-in safeguards and protection mechanisms that prevent the servo actuator from breaking down in harsh situations common to outdoor mobile robotic applications.
Field Replaceable Parts
Servosila Robotic Arms are constructed in such a way that most repairs can be done in the field by swapping relatively large self-enclosed parts such as servo actuators or grippers. The replacement operation can be carried out in the field with a screwdriver, no soldering required. All external and internal watertight connectors can be detached by hand. These features simplify repairs and maintenance, reduce the total cost of ownership, and ensure a continuous operation of the overall robotic system in the field environments where support and maintenance infrastructure is not readily available.
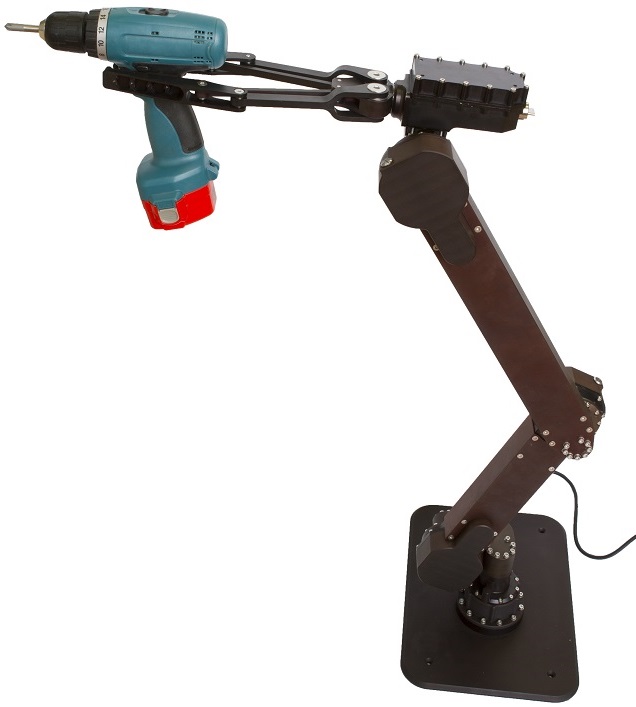
Configuration Options
Your customized configuration of Servosila Robotic Arms can be tailored to requirements of a specific application or constraints of a target host mobile robotic platform. The following configuration parameters can be selected when ordering the robotic arms:
- the number of degrees of freedom (4, 5 or 6),
- lengths of every segment of the robotic arm,
- torque of every servo joint (choose a servo actuator from a catalogue),
- the number and type of wires in a cable that goes through the inside of the arm and is used to connect external payload modules mounted on the arm to a control computer of a host robotic platform,
- type of the gripper (rotating or not).
The arm is made of servo joints and rigid segments that connect them. The more joints are included into the configuration, the more degrees of freedom the arm obtains, and the more of a flexible tool the arm becomes.
A two-segment arm allows the robot to reach out much further away from the chassis, or much higher up, and enables applications such as visual automobile inspection, and handling of potentially explosive objects. Such a two-segment arm comes with either two servo joints or with three servo joints. Both of the arm configurations enable a very flexible remote object manipulation, while the arm with three-servo joints has some advantages in confined areas where the chassis motion is restricted, such as tunnels or cellars.
A one-segment arm significantly increases mission capabilities of the robot. Such a robot can raise its sensor head, and use a gripper to grab objects from the ground or tabletop. A single segment arm can come with one servo actuator joint, or with two servo actuator joints. A single-segment-arm configuration can be enhanced by adding a gripper, or a rotating gripper. The rotating gripper allows the robot to rotate door handles to open doors in buildings. The gripper enables robots in such a configuration to perform many kinds of disaster response or public safety missions including removal of dangerous objects from populated areas.
Specifications: Servosila Robotic Arms
Parameter | Value |
---|---|
Degrees of Freedom | 4, 5 or 6 |
Maximum Lifting Capability | 4kg, 6kg or 8kg |
Input Voltage | 12-36VDC (on board)
or 220/110V AC (on a desk) |
Nominal Input Voltage | 24VDC |
Control Interface | CANbus physical
CANopen application protocol |
Max Consumed Power | >150-300W depedning on configuration |
Protection Class | IP68 |
Operational Temperature | -20C … +65C |
Weight | 7-9kg depending on the chosen number of degrees of freedom |