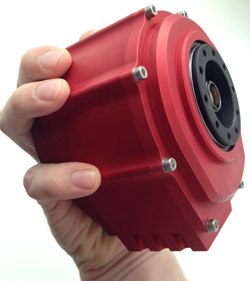
- Lightweight yet Powerful Servo Actuators. Servosila Servo Actuators feature a significantly lower weight for a given torque. The lower weight of servos increases mobility of the robotic system, reduces overall power consumption, improves motion dynamics and reduces the risk of serious injuries due to hits by moving robotic arms.
- Built-un Intelligence. The servos are controlled via a CAN bus (optionally, via PWM) with a realtime telemetry feedback and automatic health checks.
- Hollow Shafts. The servo actuators have either hollow shafts or pass-through connectors for power and control bus cables. These features are specifically introduced to facilitate robotic arm designs. The cables hidden inside a robotic arm with a hollow shaft servos are well protected from possible damage caused by outdoor use.
- Protection rating IP68.The servo actuators are watertight, work in dust, rain and snow. Extended temperature range options are available.
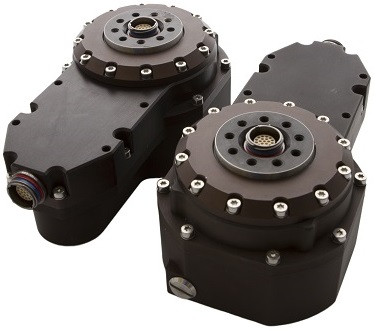
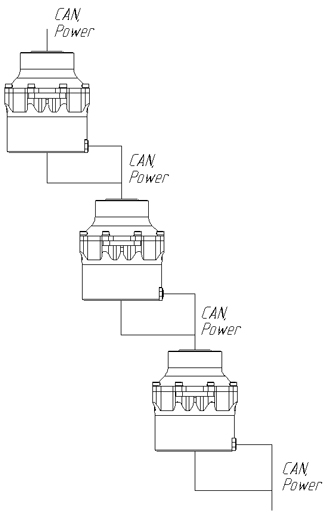
Servosila Servo Actuators are specifically designed for outdoor mobile robotic applications such robotic arm manipulators or antenna positioning systems.
The hollow shafts of the servo actuators simplify design of the robotic systems. Cables including a power bus, a CANbus network or an Ethernet network can be routed through a chain of servo actuators. Rotating joints of robotic arms based on the servo actuators hide the cables inside and reliably protect them from harsh outdoor environments. Reliability of the overall robotic system is improved due to better protection of the cables and their connectors.
The servo actuators come with water- and dust-proof connectors suitable for outdoor use. The connectors simplify replacement of faulty parts in the field without special tools thus ensuring continuous operation of the robotic system.
A standards-based CANbus network interface with a CANopen application protocol and an integrated controller board make it easy to interface the servo actuators to an onboard control system. Low weight of the servo actuators make them well suited for mobile robotics applications where weight is always at premium.
Up to 15 servo actuators can be connected in a chain with a unified CANbus network and a power supply cable. An integrated power management module enables reconfiguration of your robotic system in the field.
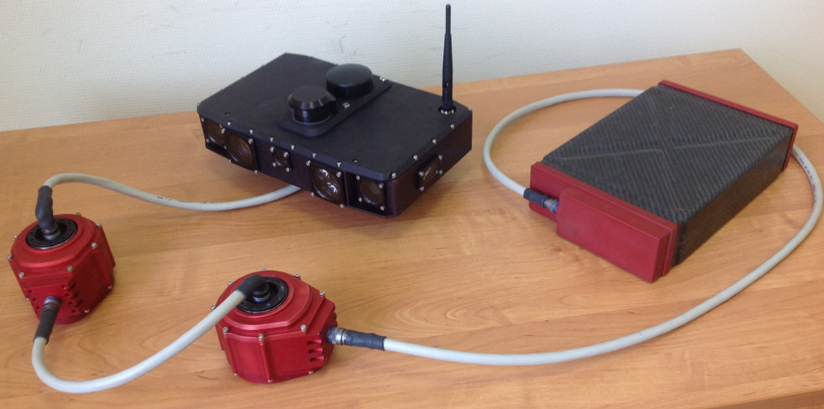
Servo Actuator 35Nm |
Servo Actuator 56Nm |
Servo Actuator 64Nm |
|
Torque, Nm | 35.0 | 56.0 | 64.0 |
Weight, kg | 1.0 | 1.0 | 1.25 |
Dimensions, mm | |||
CAD model (*.STEP file) | download | download | |
Hollow shaft | A built-in cable passes through the shaft. | A built-in cable passes through the shaft. | A built-in cable passes through the shaft. |
Speed (90°, sec) | 4.2 | 6.0 | 9.0 |
Precision, deg | ± 0.2 | ± 0.2 | ± 0.2 |
Input voltage, VDC | 18-36 | 18-36 | 18-36 |
Nominal voltage, VDC | 24 | 24 | 24 |
Average power consumption, W | 32 | 32 | 32 |
Max.number of servo actuators connected in a single chain | 15 | 15 | 15 |
Control bus | CAN (options: RS232 or PWM) | ||
IP class | IP67 (dustproof, waterproof) | ||
Operating temperature, °C | -20…+65C |